How energy storage system evolution is driven by cell chemistry - and control electronics
As the digital age advances, we are increasingly surrounded by – and dependent upon – electronic devices of all types and sizes. And, whether they are the smart watches on our wrists, the electric vehicles (EVs) that we drive, or the renewable energy sources and data centres that bring us large-scale power and IT resources, all depend on stored energy for one reason or another.
Some need this stored energy to operate, while others use it as a time-shifting buffer between grid power availability and user demand. In both scenarios, though, the devices are supplied by an energy storage system (ESS). This comprises a battery controlled by an electronic battery management system (BMS).
All device designers are under constant pressure to improve their products’ performance, functionality, and reliability while reducing size, weight, cost and energy consumption. Well designed ESS systems can contribute significantly to these goals, and their contribution can be improved both by advances in battery cell chemistry and in BMS electronics design.
This article looks at both aspects of ESS systems – cell chemistry and control electronics – and at how the latest developments in both technologies are enabling exciting progress in the products that use them. However, it recognises that different applications have very different priorities. For example, ESS size and weight saving is paramount in an EV design; in a static renewable energy storage installation it is still important, but lower priority.
Accordingly, we start by reviewing the fundamentals of cell chemistry and BMS systems. Then we look at diverse ESS applications, their specific challenges, and how the latest ESS developments are overcoming these.
Batteries and cell chemistry
Cell chemistry is the foundation of energy storage systems, and it determines the performance, safety, and cost of the system. The most common types of batteries used in energy storage systems are lithium-ion (Li-ion) batteries, which are known for their high energy density, long cycle life, and low self-discharge rate. Li-ion is of major importance because, in addition to its basic form, it has been developed into many derivatives, each offering a unique balance of benefits.
Below is a brief overview of some of the most important LI-ion variants :
Lithium Cobalt Oxide (LCO): LCO is one of the most commonly used cathode materials in Li-ion batteries. It has a high energy density, which makes it ideal for use in portable electronics.
Lithium Manganese Oxide (LMO): LMO is another popular cathode material known for its stability and safety. It has a lower energy density than LCO, but it is less expensive and more environmentally friendly.
Lithium Nickel Manganese Cobalt Oxide (NMC): NMC is a newer cathode material that offers a balance between energy density, power output, and safety. It is commonly used in electric vehicles and other high-performance applications.
Lithium Iron Phosphate (LFP): LFP is known for its long cycle life, excellent thermal stability, and safety. It has a lower energy density than other cathode materials, but it is less expensive and more environmentally friendly.
Lithium Nickel Cobalt Aluminium Oxide (NCA): NCA is another newer cathode material that offers high energy density and power output. It is commonly used in electric vehicles.
Lithium Titanate (LTO): LTO is known for its long cycle life, excellent thermal stability, and safety. It has a lower energy density than other cathode materials, but it can charge and discharge quickly.
Solid state batteries: An emerging alternative to Li-ion and lithium polymer technology offering great promise is based on solid state batteries - a new type of rechargeable battery . It uses solid electrodes and a solid electrolyte, instead of the liquid or polymer gel electrolytes found in lithium-ion or lithium polymer batteries . They have a higher energy density, charge faster, have an extended lifetime, and are much safer compared to conventional batteries . The solid electrolyte can comprise ceramics, glass, sulphites or solid polymers.
Solid-state batteries are still in the research and development phase, but they could potentially revolutionise the battery industry. They could be used in electric vehicles, smartphones, laptops, and other electronic devices. Toyota appears to be close to a manufacturing breakthrough that could accelerate the transition to electric vehicles .
Basic Li-ion operation
Like any other battery, a rechargeable lithium-ion battery comprises one or more power-generating compartments called cells . Each cell has three components: a positive electrode (connected to the battery's positive or + terminal), a negative electrode (connected to the negative or − terminal), and a chemical called an electrolyte in between them. The positive electrode is typically made from a chemical compound called lithium-cobalt oxide (LiCoO2) or, in newer batteries, from lithium iron phosphate (LiFePO4). The negative electrode is generally made from carbon (graphite) and the electrolyte varies from one type of battery to another.
All lithium-ion batteries work in broadly the same way. When the battery is charging, the positive lithium-cobalt oxide electrode gives up some of its lithium ions, which move through the electrolyte to the negative, graphite electrode and remain there. The battery takes in and stores energy during this process. When the battery is discharging, the lithium ions move back across the electrolyte to the positive electrode, producing the energy that powers the battery. In both cases, electrons flow in the opposite direction to the ions around the outer circuit. Electrons do not flow through the electrolyte: it's effectively an insulating barrier, so far as electrons are concerned.
Unlike simpler batteries, lithium-ion ones have built in electronic controllers that regulate how they charge and discharge. They prevent the overcharging and overheating that can cause lithium-ion batteries to explode in some circumstances.
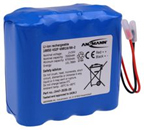
Figure 1: Ansmann 14.54V 7Ah Li-ion rechargeable battery with wire leads
Supercapacitors
Although, as their name implies, they are capacitors rather than batteries, they are worth mentioning because they make an important contribution to some ESS designs.
A supercapacitor (SC), also called an ultracapacitor, has a capacitance value much higher than solid-state capacitors but with lower voltage limits . It bridges the gap between electrolytic capacitors and rechargeable batteries. It typically stores 10 to 100 times more energy per unit volume or mass than electrolytic capacitors, can accept and deliver charge much faster than batteries, and tolerates many more charge and discharge cycles than rechargeable batteries.
Supercapacitors are used in applications requiring many rapid charge/discharge cycles, rather than long-term compact energy storage — in automobiles, buses, trains, cranes and elevators, where they are used for regenerative braking, short-term energy storage, or burst-mode power delivery. Smaller units are used as power backup for static random-access memory (SRAM).
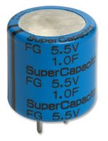
Figure 2: KEMET FG0H225ZF supercapacitor, EDLC, 2.2 F, 5.5 V, radial leaded, -20%, +80%, 7.62 mm, 1000 hours @ 70°C
Battery management system basics
A battery management system (BMS) is a device that monitors the battery’s state of health (SOH), temperature, voltage, current, and state of charge (SOC) as well as regulating the charging and discharging of a lithium-ion battery pack . It ensures that each cell in the pack remains within its safe operating voltage range, while also protecting against overcurrent, overtemperature, and overcharge conditions. The BMS typically consists of a control board with an attached display screen, as well as a number of sensors and switches located throughout the battery pack.
The control board uses information from the sensors to calculate the current SOC of each cell, as well as the overall pack SOC. It then compares these values to preset thresholds to determine when to activate or deactivate certain functions to keep the pack operating safely. For example, if one cell in the pack begins to charge too quickly relative to the others, the BMS will shut off power to that cell until it reaches a safe voltage level.
Similarly if any cells reach an unsafe temperature, the BMS will either reduce current flow or shut off power completely until temperatures return to normal. In this way, a properly functioning BMS can greatly extend the life of a lithium-ion battery pack by preventing damage caused by excessive heat or overcharging.
Key components of the BMS include:
Battery monitor which continuously monitors the voltage, current, temperature, and state of charge (SOC) of each cell in the pack. It uses this information to calculate key parameters such as capacity, power, and resistance.
Balance circuit which maintains all cells in the pack at approximately equal voltages by redistributing charge between them as necessary. This prevents any one cell from being overcharged or discharged excessively, which could damage it.
Protection circuit protects the cells from damage by excessive currents or voltages. It does this by disconnecting parts of the pack if necessary.
Control unit collects data from the battery monitor and uses it to control the balance circuit and protection circuit. It may also provide information about the pack status to an external display or computer via a communication interface.
Application examples
Having reviewed the ESS’s underlying cell chemistries and battery control electronics, we now focus on some key ESS applications.
Wearable devices
Smartwatches are just one family of a much wider range of wearable devices, which are steadily becoming more functional and popular – especially in medical applications.
As this trend continues, the need for more efficient and longer-lasting batteries is becoming increasingly important . In response, researchers are constantly exploring different materials that can improve the energy density and overall performance of batteries. For example, graphene, a single layer of carbon atoms arranged in a hexagonal lattice, has shown great promise in enhancing battery efficiency and lifespan. By incorporating graphene into wearable batteries, manufacturers can create power sources that are not only smaller and lighter but also more powerful and longer-lasting.
Wearable battery researchers also focus on the design of the batteries themselves. Engineers are working on batteries that are flexible and can be integrated into the fabric of wearable devices, providing a more seamless and comfortable user experience.
Charging convenience and simplicity is also paramount; wireless charging has emerged as a convenient and efficient solution for wearable devices. With wireless charging, users can simply place their wearables on a charging pad or dock, eliminating the need for cumbersome cables. It can also reduce wear and tear on charging ports, which are common points of failure.
There are many other ways in which battery and controller technologies can contribute to wearable development:
Solid state batteries are a promising alternative to traditional Li-ion types. Potentially, they can significantly increase wearable lifespan and energy storage capacity.
Wearable devices often have limited space for batteries, so optimizing power usage is crucial. Smart power management systems can dynamically adjust power consumption based on usage patterns, ensuring that the battery lasts longer without sacrificing performance.
Hybrid battery systems combine different battery types to maximize energy storage and efficiency. For example, a wearable device might use a combination of lithium-ion and supercapacitor batteries to provide both high energy density and quick charging capabilities.
Printable batteries are a relatively new development in wearable battery technology. These batteries can be printed onto flexible substrates, allowing for custom shapes and sizes. This opens up new possibilities for the design and integration of batteries into wearable devices.
Energy harvesting technologies are being explored to power wearables using ambient energy sources such as solar, thermal, RF, and kinetic energy. By harnessing energy from the environment, wearables can become more self-sufficient and reduce reliance on traditional battery charging methods.
In wearable devices, the harvesting scale is small, with collection fluxes measured in μW to mW. Low power design techniques are paramount, so the selection of processor, power management IC, battery, and harvester are crucial.
Renesas offers a RX111 32-bit microcontroller (MCU) which is ideally configured for energy harvesting applications, and their energy harvesting solutions can meet wearable design requirements.
The RX111 Group (See Fig.3), has a comprehensive small-capacity ROM/low pin count lineup. With USB 2.0 for Battery Charging (BC 1.2), low consumption current, and fast wakeup from standby, these microcontrollers are suitable for use in computer peripherals, and healthcare and wearable devices.
The devices offer excellent cost performance, with 50DMIPS at 32MHz. A Flash memory version is available.
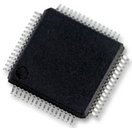
Figure 3: Renesas 32 bit microcontroller, RX family, RX100 series, RX111 group microcontrollers, 32 bit, 32 MHz
Electric vehicles
Advances in EV battery technologyWe have already mentioned the prevalence of Li-ion chemistry and some of its variants. However, with the limitations of current Li-ion batteries becoming apparent, researchers, start-ups, and automakers are racing to develop breakthrough innovations. Some of these exciting advancements in EV battery technology promise to eliminate range anxiety, shorten charging times, and make owning an EV more accessible than ever before . Here are some examples:
Carbon nanotube electrodes: NAWA Technologies has developed an Ultra-Fast Carbon Electrode based on vertically aligned carbon nanotubes. This innovation offers a significant boost in battery power, three times the energy storage capacity, and an extended battery lifespan. NAWA predicts that their technology will enable an 80 percent charge in just five minutes.
Cobalt-free batteries: To address the scarcity, cost, and environmental concerns associated with cobalt, researchers at the University of Texas have developed a lithium-ion battery that replaces cobalt with up to 89 percent nickel, along with aluminium and manganese.
Silicon anode batteries: Researchers at the University of Eastern Finland have made progress in stabilizing silicon in lithium-ion batteries. Their hybrid anode, which combines mesoporous silicon microparticles and carbon nanotubes, has the potential to significantly enhance battery performance by utilizing silicon’s higher capacity. Importantly, the silicon used in these batteries is sourced from environmentally friendly barley husk ash.
Charge your car in five minutes: StoreDot, a start-up born from Tel Aviv University’s nanotech department, has developed a charger using organic peptide compounds. This charger can recharge smartphones in just 60 seconds and is non-flammable for safer charging. StoreDot is also working on EV batteries that charge in five minutes and offer a range of 300 miles.
EV battery management’s stringent requirementsBatteries put pressure on design teams, as they need to consider priorities, including price, reliability, and safety. When handling EV systems delivering from 48 to 800 volts, you can’t risk anything.
A battery system expected to deliver more than a hundred kilowatts of energy with the push of a pedal must operate at hundreds of volts to be efficient. However, lithium battery cells supply only a few volts. To extract enough power, a large number of battery cells are connected together in series as one long stack. A typical electrical vehicle may employ 100 individual battery cells, delivering 350 volts at the top of the stack. And that presents some challenges.
If one cell dies in a long stack of battery cells, you effectively lose all of them. So, you need to monitor and manage all of them—charging them, discharging them—every day for the life of the vehicle. Lithium battery cells cannot be operated to the full extent of their charge and discharge range. They must be kept in a very specific range, such as 15% to 85%, or the cells are weakened.
ADI’s BMS provides accurate cell measurements from the time the pack is manufactured to its retirement. Electronics are attached directly to each cell in the stack, reporting back voltage and temperature, coordinated with cell current. The system figures out the state of charge and state of health. The current and temperature of every cell must be monitored through a complex algorithm at the central processor. Analog Devices (ADI) builds in a robust communication interface while allowing for a modular design architecture. It is fully extensible for their varied customer base.
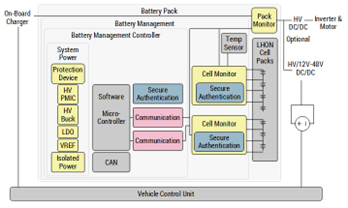
Figure 4: ADI wired battery management system
Fig.4 shows that overall supervision is performed by a Pack Monitor; ADI realise this function in their LTC2949 chip. This is a high precision current, voltage, temperature, charge and energy meter for electrical and hybrid vehicles and other isolated current sense applications. It infers charge and energy flowing in and out of the battery pack by simultaneously monitoring the voltage drop over up to two sense resistors and the battery pack voltage.
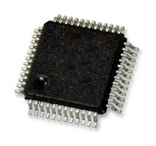
Figure 5: Analog devices LTC2949 analog devices LTC2949 battery monitor IC, multi chemistry, I2C, serial, LQFP-EP, 48-pins, -40 To 125 °C, AEC-Q100
Wireless battery management technology
Although Analog Devices supplies the market’s most accurate conventional wired BMS systems, as shown in Fig. 4, the company has been inspired to develop wireless BMS (wBMS) technology. This inspiration came from their analysis of the drawbacks of the communications wiring in conventional EV battery packs .
An EV’s battery requires a means to transfer data from each module—where voltage, current, and temperature are measured—to the electronic control unit’s (ECU’s) processor (see Fig. 6). Traditionally these connections have been made with wires: wired connections have the advantage of being familiar and well understood.
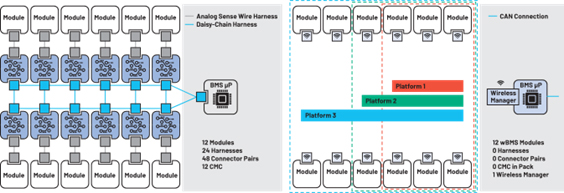
Figure 6: A typical complex, multicomponent wired BMS network (left), and the simpler arrangement made possible by Analog Devices’ wBMS technology (right).
But it is not difficult to compile a long list of disadvantages: a copper wiring harness is heavy, and occupies space that, if filled by a battery cell, would give extra energy capacity. Additionally, the connectors can potentially suffer from mechanical failure. In other words, wires increase development effort, manufacturing cost, and weight, while also reducing mechanical reliability and usable space. This results in reduced driving range.
Get rid of the wiring harness, and the car manufacturer also gains new flexibility in designing the form factor of the battery pack to fit the vehicle’s design requirements.
The battery’s wiring harness complexity also makes battery pack assembly difficult and expensive: wired packs must be assembled, and the connections terminated manually. This is a costly and hazardous process because high voltage EV battery modules are supplied charged. To maintain the safety of the assembly process and to protect production line workers, rigorous safety protocols are applied.
The advantage provided by the Analog Devices modular and scalable wBMS system platform is that an OEM can fully automate battery pack assembly. After the elimination of the (signal) wiring harness, the only connections a battery module requires are the power terminals, which can readily be made by robots in an automated process. By eliminating manual labour, OEMs also eliminate the safety risks to assembly line workers.
Solar power photovoltaic (PV) systems
Solar energy collected by photovoltaic (PV) cells is attractive as an environmentally-friendly, renewable power source. However, it isn’t ideal because sunlight levels are unpredictable, and high sunlight periods are unlikely to coincide with times of maximum demand. Therefore, it’s better to consider PV sources as a complement to, rather than a replacement for utility grid power.
This concept can be implemented using a battery and ESS system. In a simple off-grid system, the ESS system converts solar power into stored battery energy, which it then releases into the local load on consumer demand. However, grid-tied systems have now become predominant; these can supply surplus energy to the grid during periods of high generation, draw electricity from the grid during periods of low generation or high demand, and provide grid support services such as frequency regulation and voltage control, depending on the capabilities of the ESS and the system configuration.
As a critical safety feature, all grid-tied systems automatically disconnect from the utility grid in the absence of utility grid power.
PV/ESS systems use inverters to convert the PVs’ DC output into an AC voltage that can be fed into the grid or used locally. Inverter systems also participate in interfacing the PV systems with the ESS, managing the charging and discharging process.
Inverters can be implemented in different ways, usually based on either string or micro-inverter designs. Each approach has its own advantages.
Micro-inverter architectures dedicate one device to each solar panel. This approach has many advantages, including:
- A solution to shading issues
- Allow for panels on different orientations
- Increased output
- Greater safety due to lower voltage
- Individual panel monitoring
- Longer lifespan
- Easy to expand the system size
- Allows for a more flexible panel layout and expansion
NXP offers an array of products for photovoltaic inverters used in residential, commercial and utility power generation systems that supply AC power to the grid. NXP solutions enable both grid-tied systems and off-grid solar power systems. Where battery energy storage is desired, the PV inverters could be designed with bi-directional conversion and excess power can also be output to the grid .
Microcontrollers, gate drivers, power management devices and various types of wireless and wired connectivity devices are recommended for string and micro inverters (AC power output) as well as optimizer inverters (DC power output).
Fig.7 shows NXP’s implementation of a micro inverter. The company also offers string inverters, central inverters, hybrid string inverters, distributed string inverters and optimisers for PV energy generation systems.
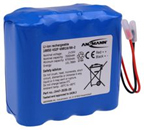
Figure 7: NXP implementation of a micro inverter
However, some users prefer string inverters over micro types, especially if there are no shading issues and several panels can be installed unidirectionally on one roof surface. String inverters have advantages of reduced wiring costs, improved redundancy, high energy efficiency, and easy replacement.
Where string inverters are preferred, their design can be improved by using Infineon’s CoolSIC™ technology. With CoolSiC™ MOSFETs, the power of a string inverter can be doubled compared to a silicon IGBT based solution at the same inverter weight. CoolSiC™ allows power density to increase by a factor of 2.5, e.g. from 50 kW (Si) to 125 kW (SiC) at a weight of less than 80 kg, so it can be carried by two assemblers. Additionally, efficiency losses at high operating temperature are significantly lower than a Si solution. Maximum efficiency is more than 99 %.
Infineon’s CoolSiC™ MOSFET 650V and 1200 V devices are cutting losses by 50% for extra energy. As the battery bank makes up the major portion of the total system costs for Energy Storage Systems, a change from silicon superjunction MOSFETs to CoolSIC™ MOSFETs can lead to approximately 2% extra energy without increasing battery size.
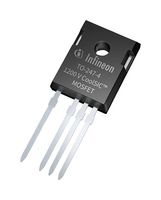
Figure 8: Infineon coolSiC™ IMZ120R140M1H 1200V SiC trench silicon carbide MOSFET
A future of continuing evolution
Batteries and ESS systems are vital components of today’s ever-evolving digital environment. Yet, new opportunities inevitably breed new challenges – and established applications always need improving as well.
Fortunately, new opportunities and challenges also drive innovation . For batteries, developing concepts include battery chemistry based on seawater, and battery technology that incorporates sand to create pure silicon.
Charging technology is also seeing innovation. For example, researchers have created a radio wave harvesting antenna using molybdenum disulfide (MoS2). This technology aims to recharge EVs over Wi-Fi by converting AC power into DC power, eliminating the need for physical charging. While the feasibility and safety aspects are still being researched, the concept holds promise for the future.
References
- Lithium-ion battery - Wikipedia
- Solid-state battery - Wikipedia
- Top Solid-State Battery Companies (ai4beginners.com)
- How solid-state batteries could transform transport (ft.com)
- How do lithium-ion batteries work? - Explain that Stuff
- Supercapacitor - Wikipedia
- How Does Battery Management System Work? - The Power Facts
- Latest Advancements in Wearable Battery Tech: Powering the Future - (lambdageeks.com)
- Energy Harvesting with RX111 MCUs | Renesas
- 2023 Top 10 Revolutionary Advances in EV Battery Technology (steerev.com)
- wBMS Technology: The New Competitive Edge for EV Manufacturers | Analog Devices
- Micro Inverters - When Do You Need Them? | Solar Calculator
- Solar Photovoltaic (PV) Energy Generation | NXP Semiconductors
- Systems and Applications - Infineon Technologies
- 2023 Top 10 Revolutionary Advances in EV Battery Technology (steerev.com)