Smart Factories: Handling complexity with flexibility
The Internet of Things (IoT) is bringing revolutionary change to industry. Smart factories that use the IoT in Industrial IoT (IIoT) or Industry 4.0 implementations are already a reality, and on a large scale. In the Siemens 108,000 square-foot Electronic Works facility in Amberg, Germany, smart machines coordinate the production and global distribution of the company’s Simatic control devices -- a custom, built-to-order process involving more than 1.6 billion components for over 50,000 annual product variations, for which Siemens sources about 10,000 materials from 250 suppliers to make the plant’s 950 different products.
The endless variables and impossibly complex supply chain maze this production process requires far exceed the capabilities of a traditional factory. The IoT’s rich arrays of sensors, robust networks and powerful computing capabilities become essential to success in such environments.
Other advanced manufacturers are also committed to Industry 4.0, not only in terms of their current implementation, but also through their investment into the technology’s future. Audi, for example, believes that the challenges to come require the vastly improved visibility, control and flexibility that only the IIoT can bring.
In Audi’s view, perhaps the biggest of these challenges relates to flexible production of customised vehicles. Almost every car is ordered with some type of customisation, from body-colour mouldings to specially-sized light-alloy wheels, and demands are increasing. Additionally, new legislation is creating further demand for differing vehicle versions. As the number of variants and derivatives grows, accommodating their requirements within a rigid, sequential process becomes increasingly complex.
In response, Audi is developing manufacturing facilities that are moving away from the traditional assembly line concept and towards modular assembly. This involves small, separate workstations that allow highly flexible working routines, in terms of both time and space. Driverless transport systems move the car bodies and production parts between the workstations under the precise control of a central computer, which ensures a smooth workflow.
The workstations themselves employ a variety of robots to perform different tasks, from screw-assembling parts underneath cars to collaborative robots that pick up coolant expansion tanks and pass them to assembly workers – without any safety barrier, at the right time and in an ergonomically optimal position. In other applications, such as handling bumpers , industrial robot arms are used to save space while providing improved repeatability, shorter cycle times and continuous operation.
The success and development of this new, flexible production model depends partly on robust networking across and between all the factory’s production and associated areas, together with advanced computing capabilities. However, the technology built into the robots and driverless transporters themselves is equally critical. Accordingly, let’s look at the challenges created by these equipment types, and the technology available to meet them.
AGVs and robots
The driverless transport systems mentioned above centre on automated guided vehicles, or AGVs. One type is controlled by a computer, while another moves autonomously along a defined route. In the Audi factory, wire and guide tape solutions are being replaced by laser scanners that help with orientation and surroundings detection, to avoid collisions. Other scanners recognise objects hanging from the ceiling.
Robots, the other key component in the smart factory example, divide into three main types; the longest-established are referred to as industrial robots. These are fixed-location devices used for tasks such as welding, painting, picking and placing, assembling, and loading objects onto pallets or into containers. Control signals come from a control cabinet next to the robot. Industrial robots are designed to perform tasks quickly, accurately and without direct interaction with humans. Accordingly, they are not designed to accommodate people within their working space, and have no sensors to detect human presence. Instead, they operate within walls, light curtains or arrays of floor mats and de-activate immediately if any of these safety barriers are transgressed.
Collaborative robots are the second type, and have the most complex interactions with humans. A collaborative robot might hold an object while a worker inspects it, or perform fine-tuning tasks. The robot might then place the object where another robot can pick it up, possibly to move it in collaboration with a different worker.
This close interaction means that collaborative robots must maintain an elevated level of environmental sensing and redundancy to quickly detect and prevent possible collisions. If a sensor connected to a control unit detects a collision between a robot arm and a human or other object, the control unit de-activates the robot immediately. If any sensor or its associated electronics fails, the robot also turns off. Collaborative robots can either be fixed, or mounted onto a vehicle.
Logistic robots are mobile units that typically operate in populated environments, for example fetching goods and bringing them to a packing station. These robots need a number of sensors for localisation, mapping, and collision prevention, especially with humans. Possible sensor technologies include ultrasonic, infrared and light detection and ranging (LIDAR).
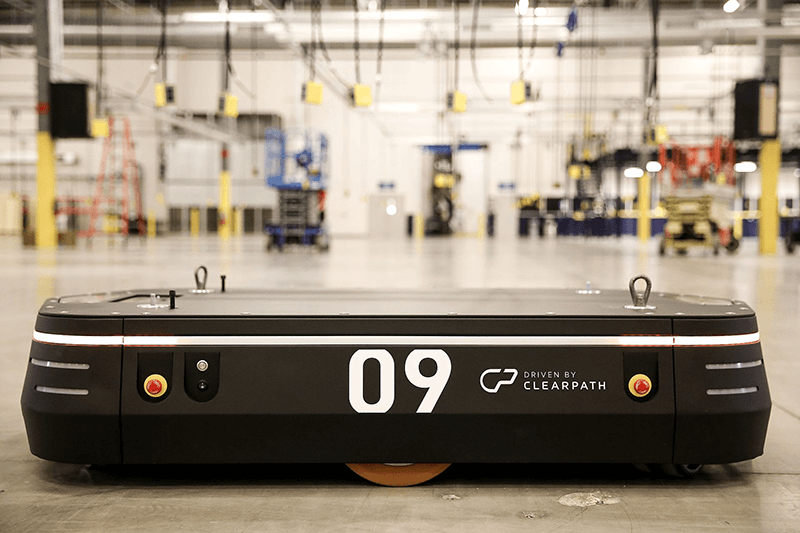
Fig.1: OTTO 1500 self-driving vehicle for heavy-load material transport in warehouses, distribution centers, and factories – Image via Wikipedia
Actuators and predictive maintenance
The driverless vehicles and robots have electric motors and other actuators that will fail without maintenance. By collecting information from sensors attached to the motors and analysing the data they provide, problems can be spotted and repairs effected before a failure and stoppage occurs.
According to Texas Instruments, a predictive maintenance system’s sensor monitoring chain comprises remote sensing with data transmission and aggregation, factory-wide real-time communications, distributed control intelligence, and access to powerful computing and analysis resources. These components function together to monitor electromechanical systems such as motors, transport systems and robots, along with field transmitters and actuators, and give warnings of probable failures that can stop production.
In traditional preventative maintenance systems, a component’s historic failure rate might be collected so that its likely time of failure can be predicted reasonably accurately. The component can then be replaced before its expected failure time – but with a good margin of error to minimise any possibility of a costly failure. This inevitably means that components are discarded with wasted working life, and maintenance intervals are shorter than they need to be; this could be improved on if only the right information were available.
Predictive maintenance is about supplying this information, collected from sensors mounted on motors or other actuators. This allows the electromechanical components to be run much closer to the true end of their working life, because the right sensor will reveal signs of their impending failure and allow a just in time response. Parameters that can be monitored for tell-tale changes include voltage, current, temperature, vibration and sound.
More data leads to better-informed decisions. Maintenance algorithms can continuously be improved, either by analysts or automatically through machine learning. Information can be fed back to parts manufacturers, leading to more robust, reliable components as well as immediate reductions in failure incidents and extensions to operational life.
Predictive maintenance components
Adding predictive maintenance capability to a motor or robot calls for several components; an article by Texas Instruments has classified these as below:
Sensors
Sensors that measure temperature, vibration, noise, voltage and current must communicate with upstream nodes, often from locations that are hard to reach or environmentally challenging. Wire connections for power and communications become impractical, so the sensors must communicate wirelessly and drain minimal power from their battery or energy harvesting circuit.
To minimise the communications and power load, sensors may include fast, granular signal conversion capabilities, and be integrated with ultra-low power microcontrollers as well as communications. Set up and provisioning functions, sensor calibration, data aggregation and storage, data filtering and pre-processing can also contribute to this minimisation.
As well as being small, robust, low power and highly functional, advanced implementations may feature multiple sensor types within a single package, to enable installation into restricted spaces.
Communications
As predictive maintenance sensors report on real-time conditions, they require fast communications with minimal latency, sometimes to defined industrial standards. Multiple protocols may be in use on the factory floor, so predictive maintenance communications should be compatible with the most widely used standards.
Predictive maintenance capabilities may not need to interface at all levels within an existing factory network; they can be added as a parallel or secondary network, with links at certain key points.
Gateways
MCUs connected to sensors typically forward the sensor data to gateways, either directly or through aggregation nodes. The gateways in turn transmit information to cloud-based resources that process, analyse and store the incoming data, and make predictive maintenance decisions. However, communications to the cloud can always be lost, so the gateway should be capable of local calculation and decision-making; issuing warnings or even initiating a system shutdown.
Gateways are also useful in large systems with high numbers of sensors. The volume of data sent to the cloud can be reduced if the gateways pre-process the data they receive before transmitting it on to the cloud. In some applications, the gateways can also perform automation and control functions.
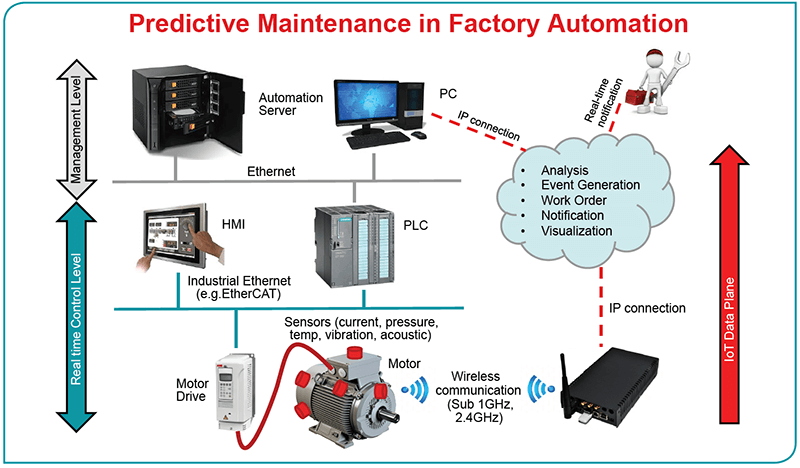
Fig. 2: Predictive maintenance in factory automation – Image: Courtesy of TI
Security
Predictive maintenance systems must be as secure as any other factory network. Sensors, data aggregation nodes, gateways and cloud-based systems must be completely secure from hacking at both software and hardware levels.
Reliability
Industrial sensors are subject to harsh environments that may include extremes of cold and heat, vibration, dirt, grease, vapor, chemicals and a variety of other potentially damaging conditions. Sensors and other maintenance integrated circuits must be characterized for use under extreme conditions to ensure continued reliability on the factory floor.
Safety
Statistically, even the most reliable sensors and integrated circuits will suffer some failures over time. Design at system level must allow for this and prevent such failures causing harm to the factory and its operators.
Precise, fast operation with safety – the role of sensors
Driverless vehicles
Each activity within an AGV’s operation cycle creates its own challenges and a corresponding demand for appropriate sensor solutions. Protection of humans is paramount as these fast-moving and sometimes heavily laden vehicles traverse the factory floor, but goods in automated areas must also be protected. The AGVs must identify goods and storage spaces, and detect free storage space. Robust communication with controlling and regulating networks is also essential.
Laser measurement systems can provide quick and accurate navigation using either space contour data, detection of reflector marks, or a combination of both . Safety functionality and collision prevention can also be added to the laser navigation system. Data from incremental encoders on the vehicle’s drive and steering axles can be used to control and limit vehicle speed.
In the loading area, photoelectric sensors can be used to control the feed conveyor, check whether the loading area is free and whether the AGV can approach without damage, and then check whether the goods have been placed onto the AGV without obstruction.
Goods on board the vehicle can carry RFID tags, containing information about the items and their packaging and pallets. RFID identification stations can collect all this data from AGVs that pass through them for storage and transfer to a central computer.
On board controllers can collect data from all of these sensors, for transmission over an industrial wireless LAN to a central computer. Integration can be eased with support for widely-accepted communications protocols such as PROFIBUS, PROFIsafe, DeviceNet, DeviceNet Safety, AS-i, AS-i Safety at Work, CANopen and Ethernet.
Robots
We have defined above the three types of robots – industrial, collaborative and logistic – found in today’s smart factories. To fulfil their promise of greater productivity and improved return on investment, all robots must perform difficult tasks with precision and complete repetitious tasks rapidly. Additionally, safety must always be part of the equation; a particularly demanding requirement for collaborative robots, which work in close partnership with, and proximity to, human workers.
Robots can also save investment on more specialised machines, and complete short production runs efficiently – sometimes for previously non-viable applications. Advanced communication capabilities, allowing data exchange between robots and with higher-level control networks, are also essential if robots are to fulfil their contribution to a fully integrated factory; an environment where more data, freely exchanged, allows better process control and maintenance, while enabling a production resource that’s more responsive to changing product demands.
Evolving robot design which meets these productivity, safety and communications objectives depends ultimately on advanced integrated circuit solutions. Overall, these solutions must provide precise sensing, high speed sensor signal conversion, fast computation and signal processing for real-time response and high-speed communications. Integrated circuit technology also facilitates the high-efficiency, small form factor power supplies needed by the sensors and computational devices.
Texas Instruments has defined the required features of integrated circuits used in robot applications as below:
- A high-efficiency, high-voltage power supply with circuit protection and low-noise emissions
- Characterization for an extended temperature range
- Support for industrial ethernet and other widely used industrial communication standards
- Ease of programming for greater flexibility
- Fast, precise analogue-to-digital and digital-to-analogue signal conversion
- Reinforced isolation to meet industrial safety standards
- Control redundancy for safety-critical applications when combined with other integrated circuits
- A small footprint when placing circuitry in tight spaces such as mobile logistic robots, or for motor control in robot arms (not to mention other equipment with tight spaces, such as sensors and motor housings)
- Low power consumption (critical for battery- or ambient-powered equipment such as logistics robots and sensors)
- Comprehensive support, including reference designs and evaluation modules (EVMs) to minimize design time and let designers focus on value-added technology.
Integrated circuits that fulfil these requirements
TI offers integrated circuits and support services within all these areas. Products cover sensor inputs and actuator and motor outputs, and communications across the entire signal chain, from equipment and workstations, to factory floor or higher levels. Features include reinforced isolation, and products are tested and qualified for use in harsh industrial environments. This coverage can be represented by the following key products and areas:
Sitara processors: These processors are designed for flexible, fast design in robots and other industrial equipment. Based on ARM® Cortex®-A cores, they provide flexible peripherals, connectivity and unified software support. A broad portfolio of single- and multicore devices offers a balance of integration, connectivity and performance. A fully scalable software platform enables a unified software experience for simplified development and code migration across Sitara processors and TI digital signal processor (DSP) families. Pin-compatible options within processor families make hardware upgrades seamless.
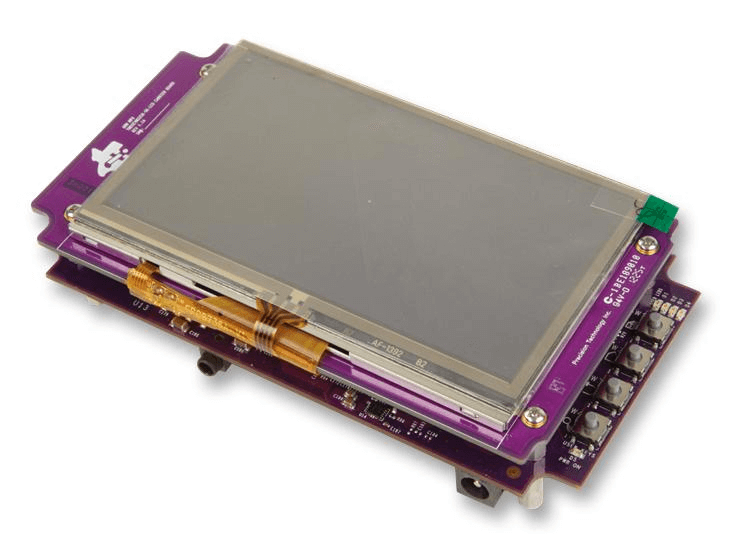
Fig.3: TI Sitara Starter Kit
Proximity sensing: TI’s sensing technology can be used to provide collaborative robots with the sophisticated sensing of nearby objects and people essential to make them safe. TI sensors are available to measure target objects’ distance as well as their presence. Sensor technologies include ultrasonic, magnetic, capacitive, inductive and Time-of-Flight (ToF). TI’s 3-D ToF chipsets allow for maximum flexibility to customize designs for robot vision and other applications.
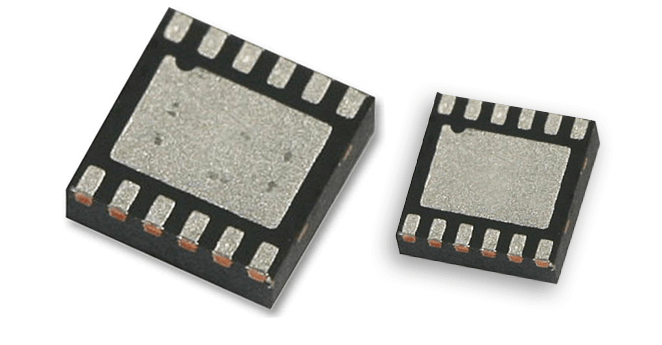
Fig.4: TI Inductive sensor
GaN power: In addition to an extensive power management portfolio of switching and linear regulators, switching controllers, power monitoring and other supporting power management devices, TI offers GaN modules, drivers and controllers that provide outstanding power density for high-voltage power supplies in industrial systems. GaN technology greatly reduces switching losses and therefore enables faster switching speeds while minimising or eliminating heat sinks.
Industrial networks: A network designed for use in industrial applications requires determinism and real-time control. Examples of Ethernet protocols that provide these features include EtherCAT, PROFINET, EtherNet/IP, PROFIBUS, Ethernet Powerlink, Sercos and others; the PRU-ICSS subsystem within the Sitara microprocessor supports these protocols.
IIoT development activities
Manufacturers offer support tools including dev kits to help designers move rapidly into the product differentiation, value-adding stage of their project development. Here are some examples:
- TI’s AM335x Starter Kit (EVM-SK) provides a stable and affordable platform to quickly start evaluation of their Sitara™ Processors
- TI also offers an EVM and a highly configurable camera development kit (CDK)
- The TIDA-00913 is a reference design that uses a GaN inverter for accurate control of precision drives such as servo drives.
- The TIDEP0061 reference design implements an applications example of a 4-axis CNC router based on the Simple Open Real-Time Ethernet (SORTE) protocol and Sitara PRU-ICSS unit.
- Analog Devices’ EVAL-CN0303-SDPZ Evaluation Board for MEMS based Vibration Analyzer with Frequency Response Compensation. The circuit provides a low power solution suitable for bearing analysis, engine monitoring and shock detection. This provides a 3-D location of each pixel for accurate depth maps that aid customization for a given application.
Conclusion
The concepts of the Smart Factory, IIoT and Industry 4.0 have futuristic overtones, but many organisations are implementing them now as well as investing significantly for the future. Productivity, flexibility and safety are the goals, while AGVs and robots of various types are making major contributions to achieving them.
These machines must function as nodes on the factory network, while performing their tasks with speed, accuracy, flexibility, safety and reliability. This article has shown how designers have opportunities to continue improving these aspects of AGV and robot performance, through the availability of advanced integrated circuits and support products. Faster, better solutions can be developed for sensing, signal processing, local processing, power management and communications. Innovative predictive maintenance designs can extend component life, improve designs for reliability, and alert operators of impending component or equipment failure before it leads to a production stoppage.
Discussing your ideas with Farnell at the outset of your project won’t cost you anything, but could save you considerable time and money. As a Development Distributor, Farnell has the expertise to advise you on developing and building your prototype faster, backed by products, test equipment and custom development services. This support continues into production, with deliveries from tape and reel services for components to spares and consumables for maintenance.
References
http://www.industryweek.com/technology/dawn-smart-factory?page=1
http://www.autoblog.com/2015/07/21/audi-smart-factory-production-4-0
http://www.just-auto.com/news/audi-adds-human-robot-cooperation-in-manufacturing_id155721.aspx
http://www.eetimes.com/document.asp?doc_id=1274020
http://www.ti.com/lit/wp/sszy027/sszy027.pdf
https://www.sick.com/media/docs/4/54/354/Industry_guide_Efficient_solutions_for_material_transport_vehicles_in_factory_and_logistics_automation_en_IM0026354.PDF
http://www.ti.com/lit/wp/slyy115/slyy115.pdf
http://www.ti.com/tool/opt8241-cdk-evm
http://www.ti.com/tool/tida-00913
http://www.ti.com/tool/tidep0061
TMDSSK3358 - Starter Evaluation Kit
EVAL-CN0303-SDPZ - Evaluation Board
Smart Factories: Handling complexity with flexibility. Date published: 19th July 2017 by Farnell element14